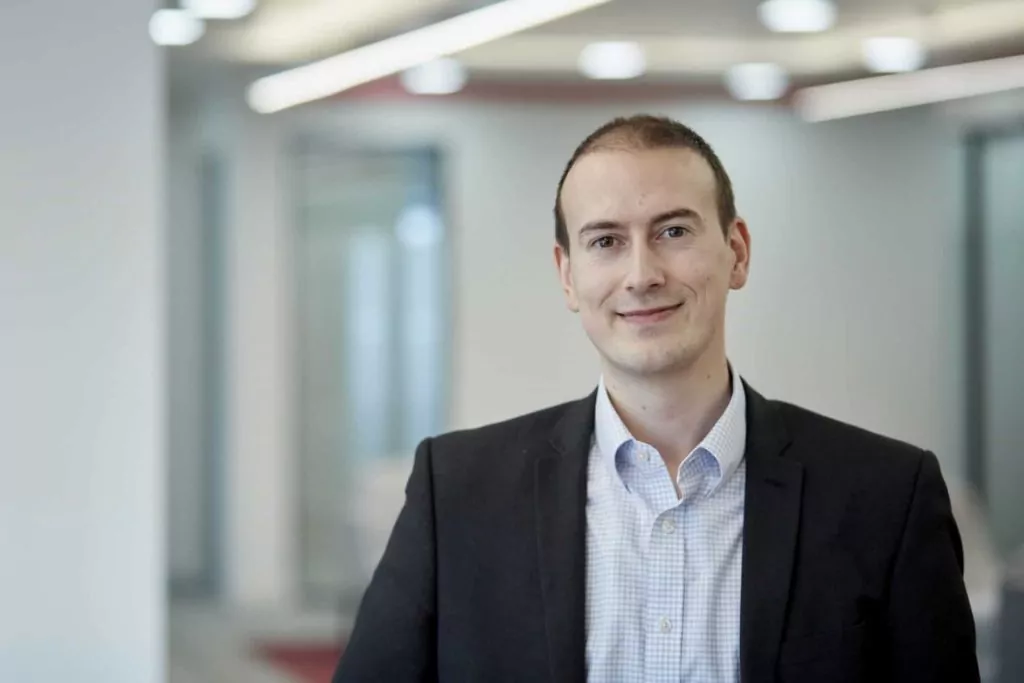
Health and safety in grid scale electrical energy storage systems
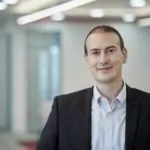
By Mark Greatholder, Aliki Zeri, Colin Shear
3 May 2024 | 3 minute read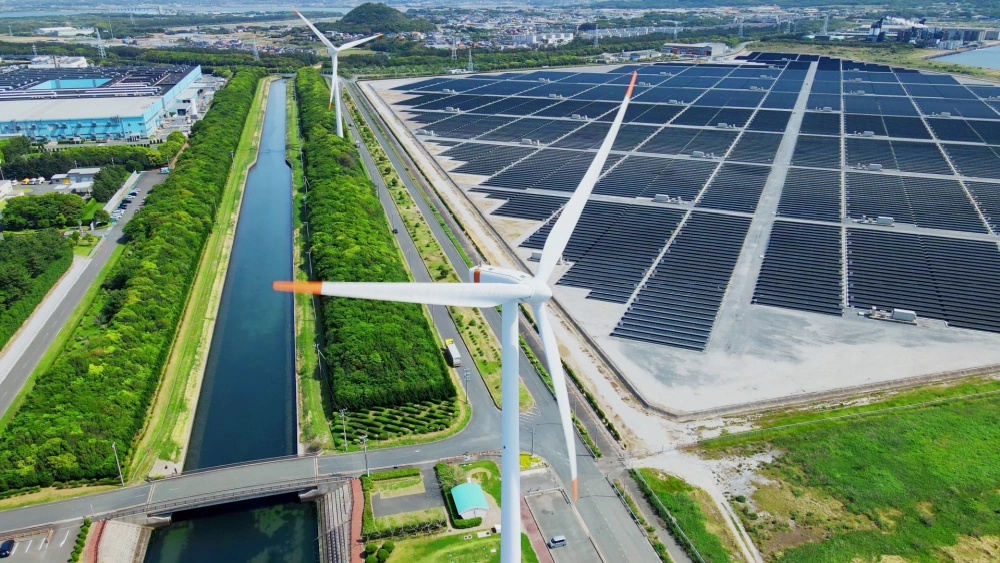
The volume of grid-scale electrical energy storage systems (EESS) connecting to our electricity system is growing rapidly. These EESSs provide a key role in the decarbonisation of the electricity system by providing enhanced grid flexibility, providing ancillary services (e.g., frequency response), maximising the usable output from intermittent low carbon generation by deferring or avoiding the need for costly network upgrades and new generation capacity, and by contributing to energy security.
It's essential that EESS are developed in line with appropriate health and safety (H&S) standards and that regulations are adhered to across the industry. The complexity of the landscape, with a plethora of standards (some with overlapping requirements), can be a barrier to this.
In April 2024, the Department for Energy Security and Net Zero (DESNZ) published guidance on health and safety standards for grid scale electricity storage systems.
By highlighting existing legislation, regulations, standards and other industry guidance, it is hoped that the guidance will help battery storage project developers navigate the H&S landscape and ensure relevant aspects of H&S are integrated into their processes.
Who is this new guidance aimed at?
The guidance focusses on ‘grid-scale’ battery applications, which for the purposes of the guidance are systems rated at 1MW and greater. The guidance is applicable to any organisation who trade in a lifecycle stage of grid-scale battery system, from design to decommissioning, as well as situations such as battery co-location with other technologies.
The guidance is also primarily targeted at variants of lithium-ion batteries, which are currently the dominant energy storage solution in the market. However, the nature of the guidance is such that elements will be applicable to other battery technologies or grid scale storage systems.
Project lifecycle
The guidance is structured around five key lifecycle stages during which health and safety risks should be identified and mitigated by stakeholders. The guidance also provides a template for identifying which stakeholders are responsible, accountable, or need to be informed or consulted to mitigate such risk throughout the lifecycle and advises that the asset owner has primary responsibility for allocating this responsibility.
This stage relates to the design, manufacture and certification of equipment, site appraisal and performance estimation. Effective assessment of potential risks is central to management of health and safety at the outset of a project.
When considering the BESS context, hazards should be considered for all stages of the system lifecycle which are applicable to the organisation (either directly or indirectly). All system components should be designed, manufactured, and tested in accordance with relevant safety standards. The integration of BESS components should also be considered when performing a risk assessment, in particular any incompatibilities between components which may present a risk to H&S.
There should be a full consideration of risks including, but not limited to, accidental or intentional damage and natural phenomena and security. Risk assessments should include both risks to the project and from the project. The planning process should assess the following risks and describe how the credible worst case has been mitigated.
Due to the potential hazards to the surroundings of any BESS, careful considerations must be made as to its location to determine the risks that the storage proposes. With lithium-based technologies, thermal runaway is a key failure mode which can lead to hazards to the nearby environment.
There should be a full consideration of site/ project risks including, but not limited to, accidental or intentional damage and natural phenomena such as fire, weather (including snow and ice and access during severe weather), flooding, land subsidence, flora, and fauna (including birds and mammals), and security.
Co-locating energy storage with energy generation is becoming increasingly common. Energy storage could be co-located with solar panels, wind turbines, hydroelectric generators, hydrogen production facilities, storage or different battery technologies. Where there is the potential for co-location, additional risk assessments need to be undertaken for the combination of technologies at a given site and the potential propagation of hazards.
Where multiple generation, storage or industrial facilities are located in close proximity (but not necessarily co-located in such a way as to pose a direct risk to one another), consideration should also be given to the local capacity to deal with multiple concurrent issues and the implications for emergency response.
This stage relates to the preparation and execution of the physical movement of equipment/assets between locations. The preparation and transport of BESS equipment can pose various logistical challenges and safety risks and as such should be considered in the context of health and safety. The preparation and transport of BESS equipment must have the same level of protection as it would once installed.
BESS developers should consider access requirements for equipment transportation, which may include heavy or oversized vehicles requiring wider or stronger access routes than will be needed during normal site operation. This should extend not just to the site itself, but to surrounding roads and routes from nearby trunk roads that equipment will be transported on. Where oversize loads (e.g. transformers) are being transported consider whether special signage or escort vehicles may be required.
This stage covers the physical installation, training, and connection of assets at their intended location and connection to their respective interfaces. It also covers inspection, testing and training for operators and handover of the system from installer to operator and the post-handover tuning/ bedding-in period. Project management and governance is particularly important here, as correct mitigation of risk will ensure robust health and safety measures are in place at this stage. Recommendations include health and safety training to all relevant staff, as well as due diligence on potential contractors, and ownership of hazards across the project.
During the installation and commissioning phase it is possible that safeguards planned for the final site configuration, such as fire detection and suppression systems, will not yet be in place. Developers should consider how hazards may arise or evolve during this stage, and whether temporary mitigations such as portable fire detection/firefighting equipment are required.
Commissioning consists of a series of steps to demonstrate, measure and record component and system performance. Commissioning processes include sets of tests, checklists, specifications, standards and procedures to validate performance and identify and correct problems before a system becomes operational. The guidance sets out a helpful overview of the range of activities which could be expected to be undertaken during commissioning, many of which have implications for system safety.
This stage relates to usage, inspection, testing and upkeep of the system and may include periodic verification of system safety by a third party e.g., manufacturer or regulator.
Safe operation will be supported by a range of operational and safe working practices. The plant should only be operated by skilled personnel and output should be maintained within operational limits. Site access should be limited to authorised personnel, site safety rules should be in place and policies and processes adopted to maintain site cybersecurity.
Bringing together the various safety plans, features and monitoring systems discussed across previous sections, safe operation will include continuous monitoring of equipment across the site (batteries, inverters, transformers etc) to detect abnormal operation or indications of emergent faults and monitoring of CCTV to ensure site security. Escalation plans should be in place to respond to potential hazards, including out of hours support.
There should be an asset management strategy in place which details appropriate equipment inspection, preventative and reactive maintenance requirements and the methods through which equipment defects are assessed. This may include multiple inspections or maintenance and testing intervals throughout the year to ensure all parts of the system are in working order and system settings (e.g., electrical protection) are correct.
During the life of a BESS there may be the need to make unplanned changes to its design or operational arrangements. In these cases, many of the principles discussed earlier in the document around risk assessment around any redesign, installation, commissioning, operation and maintenance apply.
This stage relates to the preparation and execution of permanent shutdown and disconnection of the system and its components, the removal from the installation site, restoration of the land, re-use and recycling or disposal in accordance with waste equipment regulations.
The decommissioning of a BESS site presents similar health and safety risks to its commissioning, due to changes in the site’s operation and potential removal of safeguards.
The Waste Batteries and Accumulators Regulations 2009 require that “industrial batteries” – a definition that applies to BESS li-ion cells – must be sent for recycling by an approved operator. Distributors of industrial batteries are also obliged to take back waste cells free of charge when requested by the end user. BESS developers should consult with proposed battery suppliers at an early stage to establish their processes for take-back and recycling, and to ensure as far as possible that these schemes (or equivalents) will be available at the predicted end of site life.
Developers should also be aware of the Waste Electrical and Electronic Equipment Regulations 2013, which imposes broad obligations on the recycling of electronic products. While the core equipment of a BESS site may not meet this definition, many items installed on site will – examples may include computers and display equipment, monitoring, control and communication instruments and lighting equipment.
How does this guidance impact your BESS projects?
The guidance focuses on the health and safety aspects of grid scale battery system development, drawing on both national and international standards and guidance documents to highlight current good practice. It is however not a guide on battery project development, and it does not cover the standard planning and consenting process for battery system developments. Furthermore, it does not comment on any ongoing regulatory changes such as those related to Brexit or the establishment of a UKCA marking regime.
However, by highlighting existing legislation, regulations, standards and other industry guidance, it is hoped that the guidance will help battery storage project developers navigate the H&S landscape and ensure relevant aspects of H&S are integrated into their processes.
It should be emphasised that what is presented within this document is not a prescriptive checklist of activities and it is the responsibility of the overall duty holder (typically the owner and operator employer of the asset) to apply guidance to their specific project, comply with the relevant laws and take into account relevant standards.
The industry-wide understanding of risk assessment and reduction, emergency response arrangements and best H&S practices for all stages of the system lifecycle is constantly developing but lagging behind the pace of technology development. This makes it difficult to know the benchmark for H&S in the context of grid-scale storage systems, and how to continually improve and ensure compliance with relevant standards at all times.
Developers should take steps to fully understand the relevant H&S standards that they must adhere to when looking to develop a new BESS project and stay on top of any developments in this area. Developers of projects already underway should also consider undertaking an assessment of their current projects to determine whether they continue to meet the evolving standards of best-practice and/or whether any changes ought to be made to ensure that those projects remain compliant from a H&S perspective.
Get in touch
Our team of experts at Foot Anstey are on hand to help clients navigate through the health and safety regulatory landscape as the market for energy storage evolves. If you have any queries or require any support, please get in touch with a member of our team.